DIRECT TO FILM SHAKERS
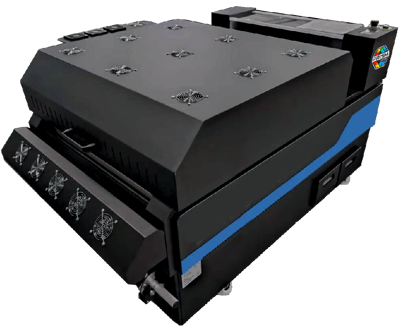
32" Powder Shaker
- Maximum Film Width - 31.5” (80cm)
- Power Requirements: Single Phase 220v, 30a
- Warranty: One year
- Machine Size: 76” L x 54”D x 45” H
- Machine Weight: 840 lbs.
- Minimum Door Clearance: 55”
- External fume extractor is optional based on environment.
This 32" Shaker/ Dryer unit is designed to seamlessly pair with the Mimaki DTF printer. Your prints will have the powder evenly applied, and cured on a system that will keep your environment safe and comfortable. The cooling fans and take-up roll will keep your prints looking perfect until you are ready to cut and apply them to your products.
- Control Panel - All-In-One PLC Control Touch Panel for ease of operation and automatic production.
- Integrated Internal Smoke Purifier - The strong purifier is designed to make the DTF process more environmentally friendly.
- Two-Sided Heater - Lamps on both top and bottom regulate the temperature gradually. The bottom heater slows down ink drying by gradually increasing the temperature while the top heater accelerates powder melting by gradually decreasing the temperature to ensure even powder application and curing
- Intelligent Heater Control - Saves 30% power by automatically turning off the heater when it reaches the desired temperature and prevents the film from overheating if the machine pauses or stops operation.
- Powder Recycling - Both left and right side powder recycling to maximize equipment positioning.
- Powder Removal - 4 Stage Vacuum with a high-frequency powder removal system helps remove powder from non-inked areas of the film.
32" Powder Shaker II
- Maximum Film Width - 31.5” (80cm)
- Power Requirements: Single Phase 220v, 30a
- Warranty: One year
- Machine Size: 64” L x 36”D x 49” H
- Machine Weight: 625 lbs.
- Minimum Door Clearance: 32”
- External filtration or venting is required
63” Powder Shaker
- Maximum Film Width - 61.02” (1.55m)
- Power Requirements: Single Phase 220v, 30a
- Warranty: One year
- Machine Size: 124.25” L x 85”D x 43”H
- Machine Weight: 1370 lbs.
- Minimum Door Clearance: 88”
- External filtration or venting is required
FLATBED CUTTERS
32" or 63" Wide Roll to Roll Cutter
- Integrated Roll to Roll feeding system
- Full or half (perforated) cut patterns
- Max Cutting Speed: 600mm / second
- Utilizes the Gunner Cut Driver
- 1 Year Warranty
8090F
- 32” x 35.5” flatbed cutting area
- 71” L x 52” D x 41” H
1612F
- 63” x 47” flatbed cutting area
- 87” L x 82” D x 41” H
FUME EXTRACTORS
JS160 Extractor
- 33" wide or larger equipment
- Electrical Connection: 220v / 10a
- Airflow: 1200m³/h
- Machine Size: 28.5”W x 27.5”D x 66” H
JS100 Extractor
- 32" wide or smaller equipment
- Electrical Connection: 110v / 10a
- Airflow: 660m³/h
- Machine Size: 21”W x 22.5”D x 54” H
How to Achieve Softer DTF Prints
Do Your DTF Prints Feel Plasticky & Lack Breathability?
While DTF printing allows businesses to attract garment decoration clients with intricate details, vibrant colors, low costs, and fast delivery, achieving softer DTF prints can provide an additional advantage and help your business stand out from the competition. Although it may require some knowledge, experience, and techniques, with learning and practice, achieving great results is definitely possible. In this post, we’ve organized the top 10 proven tips for DTF printing users and business owners to make their transfers softer and more breathable, elevating their printing business to the next level.
The heavy and plasticky feel of DTF prints is due to how the DTF printing process works. Instead of printing directly onto the garment, DTF printing uses white ink as a base layer and adhesive powder to adhere the prints. Therefore, the primary reason your DTF prints may feel plasticky or stiff is that the white ink layer is too thick and the prints have received too much powder.
In addition to these factors, several other elements might also affect the softness of your prints, including:
- The quality and thickness of the transfer film used
- Pressure and heat settings during the transfer process
- The type of fabric being printed on
- The specific ink used
Don't Use Inferior Consumables
To achieve softer prints, it’s crucial to use high-quality ink and film. Inferior materials can lead to a rough, undesirable texture. The color layer of the film plays a significant role in determining how much ink and powder are applied during printing. If the film and ink absorb too much powder, the prints can end up feeling thick and plasticky. The coating on the film also plays a crucial role. A heavy coating can transfer onto the shirt, resulting in a thick, heavy feel. Conversely, if the coating is too light, the ink may not adhere properly to the film, leading to poor print quality. Opting for premium materials helps ensure you achieve the desired softness and quality.
Adjust Ink Levels
Use the appropriate amount of ink, as too much can make the print feel heavy and stiff. Adjust the ink levels in your RIP software to avoid overloading the film, especially for the white ink base layer.
You might start by testing with a reduced underbase thickness of 50% to minimize the transfer’s plastic-like feel. However, be cautious; removing too much white ink can result in faded colors. Thus, it’s crucial to experiment with the settings to find the right balance between vibrancy and softness.
Knockout Black, add Halftones
Black knockout and halftone are two creative and powerful techniques to enhance prints. Black knockout is a technique that works best on dark-colored shirts that involves removing most of the black ink from a design to make shirts more breathable and softer.
Halftone printing creates an optical illusion; the size, shape, and spacing of the tiny dots are blended into a continuous tone by the human eye. The result is an image with a softer, more complete visual appearance. It is another effective techniques to enhance hand feel of DTF prints. Instead of using solid blocks of color, which can feel heavy and plasticky, halftone uses varying sizes and densities of dots to reproduce shades and gradients. This technique reduces the amount of ink and enhances DTF print hand feel by enabling smoother color transitions, reducing overall ink build-up for a lighter feel, improving the flexibility of the print to prevent cracking, and creating a more natural texture that feels softer and more integrated with the fabric.
Pre-Press the Garment
One best practice for garment decoration with DTF printing is to pre-press the garment for a few seconds before applying the transfer. This step removes moisture, allowing inks and powder to interact more effectively with the material for a softer feel. Additionally, pre-pressing eliminates wrinkles, ensuring the prints receive even heat and pressure distribution, which results in a smoother finish.
Press a Second Time
This is one of the most popular and effective solutions for achieving exceptionally soft and breathable DTF transfers. A second press can help further embed the ink into the fabric, resulting in a softer and more integrated feel. While some DTF sellers may claim that transfers only need one press, a second press can make a significant difference.
A second press serves several purposes. Firstly, if your prints look shiny, a second press can give them a more matte or retail appearance. Secondly, if your transfers have too much powder, a second press can burn off the excess powder and embed it better into the material. Lastly, a second press helps set the inks into the fabric more effectively, improving the prints’ washability and durability.
Try Multiple Cover Sheets
During the second press, you have several options for the cover sheet, including Teflon sheet, parchment paper, butcher paper, spare t-shirts, or silica mats. Each of these materials can impart unique characteristics to your DTF transfers. To achieve the best results for your projects, it’s beneficial to experiment with these different cover sheets. This experimentation allows you to select the one that best suits your specific needs and preferences, ensuring a superior and customized experience for your customers.
Proper Powder Application
A major cause of heavier, plastic-like prints is the excessive application of powder, which can be influenced by printer settings. For instance, our DTF printer is equipped with both front and rear heating areas, where the front heating helps dry the ink slightly to prevent it from absorbing too much powder. Additionally, removing excess powder from the transfer is crucial for achieving a consistent, soft texture. This is best accomplished with an industrial shaker, which should be properly set up and equipped with a pre-heat function to ensure the film receives the optimal amount of powder, avoiding a heavy, plasticky feel.
Proper Curing
Another important tip is to make sure the ink is properly cured. Under-curing can leave the print feeling sticky, while over-curing can make it feel stiff. Follow the recommended curing times and temperatures for your specific ink and film.
Choose the Right Fabric
Different fabrics can impact the final hand feel of the print. For example, cotton typically offers a softer feel due to its natural fibers, which absorb ink and powder more evenly. Polyester, on the other hand, may provide a slightly less soft feel because synthetic fibers are less absorbent. Blended fabrics, like cotton-polyester, offer a balance between softness and durability. When selecting fabric for DTF printing, consider factors such as composition, color, texture, weight, and stretch.
Fabric Type | Key Properties | Suitability for DTF Printing |
---|---|---|
Cotton | Breathable, absorbent, soft | Excellent adhesion and vibrant prints |
Polyester | Low moisture absorption, smooth surface | Highly compatible with vivid, clear prints |
Silk | Durable protein fibers, natural shine | Suitable for creating luxurious, elegant designs |
Leather | Durable, flexible, authentic appearance | Ideal for bags, belts, and accessories |
Denim | Diagonal weave, combed cotton | Excellent for casual and complex designs |
Nylon | High elasticity, abrasion resistance | Suitable for workwear, bags, and sportswear |
Blended Fabrics | Combine properties of different fibers | Offer a balance of comfort, durability, and print quality |
10. Experiment , Test, & Record
Each printer, material, and setting can behave differently, so it’s crucial to experiment with various combinations to achieve the softest hand feel. Testing different settings and materials helps identify the optimal setup. It’s highly recommended to keep detailed records of your equipment settings and consumable choices. This documentation will make it easier to pinpoint the best combination and replicate successful results in the future.